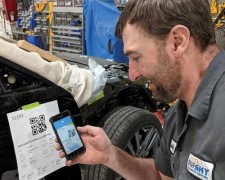
CARLSBAD, Calif., July 30, 2019 (Newswire.com) - NOTE: This June SPS was originally published online in May 2019.
More than 40 years ago, Matt McDonnell Sr. established Big Sky Crash Repair out of a four-car garage in Billings, MT.
The business’s name later changed to Big Sky Collision. Fast-forward to 2019, and the company has grown to be the largest family-owned collision repair facility in its area.
Matt’s son, Matthew Jr., joined the team about a decade ago. After working alongside his older brothers for a few years, Matthew bought them out in 2015.
By August of that year, the company had purchased a second location in Bozeman and soon after opened a third in Livingston.
In addition to its extensive OEM certifications and keeping up with the latest developments in tools and equipment, McDonnell said part of the company’s success is due to a strong emphasis on leadership training.
“We’ve noticed that very few shops in the country train,” he said. “They might bring in consultants, but they don’t set aside time for estimator training, CSR training or anything else along those lines.”
As a result, he said Big Sky has focused on targeted training for all employees based on the business goals CCC has helped put into place.
Big Sky has used CCC® Estimating software for decades. Last year, it incorporated more features in the CCC ONE® Total Repair Platform to help boost performance. McDonnell said customers now have expectations that are created from other buying experiences, such as Amazon and the doctor’s office, and CCC products are helping the business meet these expectations.
The software includes CCC® Repair Workflow, a configurable business tool designed to streamline operations, and CCC® UpdatePlus, which has enabled the shop to automate appointment reminders for customers and send repair status updates via text or email.
The shop also uses CCC® Lobby, which allows customers to electronically confirm their information when they walk into the shop. They can select their preferred method of communication rather than filling out paper forms and information they have already provided to the insurance company.
“Our customers love the lobby check-in process, which is a tablet check-in form that guides them through critical questions,” said McDonnell.
With goals in place to facilitate the MSO’s continued growth, Big Sky recently became involved in CCC® Elevate. The personalized CCC consulting service is designed to help collision repairers better understand and achieve their overall business objectives and help optimize their processes.
This includes defining staff roles, demonstrating ways to improve the overall customer experience and creating personalized Standard Operating Procedures (SOPs).
Many times, McDonnell said it can be challenging to optimize business practices when writing manual SOPs. CCC Checklists is helping Big Sky meet this challenge.
The fully customizable tool enables collision repair shops to set the tasks they want completed, track quality control and document the quality of the repair. The management tool uses electronic SOPs and automatic logging. It also can store photos, notes and reports.
“Using CCC’s Total Repair Platform, we are able to create quality control checklists that are incorporated into the repair plan,” said McDonnell. “There are critical processes (like photos or repair procedures) that need to be completed before the technician can move the vehicle.”
For example, if they have a sectioning procedure, the checklist requires photos of the welds and sectioning area before the vehicle can be moved to the next stage in the repair process.
Since using CCC® Checklists over the last year and a half, McDonnell has found that it has empowered his employees with the tools they need to provide excellent service. Working with CCC, they have been able to define their unique operational processes and enable their locations to set high standards for the business. Checklists then holds employees accountable for their work to ultimately ensure each store is repairing vehicles correctly every time.
“Checklists is a wonderful tool,” said McDonnell. “It makes sure that as you go through the process, you have a direction.”
Big Sky created its own checklist of features to ensure technicians provide a “bullet-proof” repair. All of McDonnell’s technicians have downloaded Checklists on their phones in order to keep track of action items to address during each stage of the repair process.
“It creates a chronological order of things that have to be done in order to move to the next step,” said McDonnell. “It really makes sense and I love it.”
McDonnell said CCC’s extensive support and high-quality products are helping position the collision repair business for future growth. This is important, as the company plans to add additional locations over the next several years.
“We have a winning attitude and culture at Big Sky. We have some really good people working for us with the right attitude and leadership qualities, and it’s contagious,” said McDonnell. “We’re never going to give up, so we never take defeat. Instead, we learn from what we did and get better.”
He said CCC is helping him and his team meet their business goals, and they have been impressed with the attention given to their business.
“It’s extraordinary,” he said. “We receive unbelievable customer service from CCC.”
Big Sky Collision (Network)
Location: Billings, MT
(406) 259-6328
www.bigskycol.com
Company At A Glance...
Type: Collision Repair
Facility Employees: 70
In Business Since: 1978
Number of Locations: Three
DRP Programs: Two
Combined Production Space:
2 city blocks
CCC Information Services, Inc.
(877) 208-6155
www.ccc-one.com
Source: Autobody News
Share: