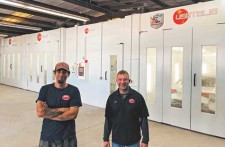
CARLSBAD, Calif., December 18, 2018 (Newswire.com) - NOTE: This June SPS profile was originally published in print in June 2018 and online in May 2018.
Rich Lendino is the head painter at Martin’s Collision Center in Sanford, FL. The company also owns and operates its sister location, Sanford Body & Paint.
With USI North America's EPS System, per vehicle, we're saving roughly 25 minutes every cycle, which is definitely significant. Essentially, you enter the job's parameters in the system and it tells you the best way to paint the car.
Rich Lendino, Martin's Collision Center
In many ways, Lendino was born to be a painter and knew early on it was the right path for him to take.
“I painted my first car, a Ford, when I was 13 years old, and after that I was hooked,” he said. “My dad was an insurance adjuster in New York, where I’m originally from, and we spent a lot of time together out on the road visiting shops. I started working at a shop as a clean-up guy, and then one day a painter didn’t show up for work, so I got my chance. They had me doing cut-ins, and then after a few weeks they stuck me in the booth and said, ‘Go at it.’ I haven’t stopped painting since.”
When Lendino started in the industry 23 years ago, there were a lot of veteran painters out there, but now many of them have retired and there aren’t enough new people to fill the void, he said.
“If you’re a young person and want a great career, this can be it, because you can make good money and a decent painter will always be employable,” he said. “We have people here who started out as drivers and preppers, and now they’re painters. My advice is to develop an eye for detail; stick with it and be passionate about whatever you’re doing and you will succeed. Get the training from the old school guys the way I did. You can spend hours and hours in a classroom, but the best way to learn is by doing it yourself in the booth with a good teacher. That’s why I’m a huge believer in hands-on training.”
Lendino played an integral role in finding his company’s new booth when their former booth was ready to retire.
“When I first got here, we had a few older booths, but the owner, Dave, told me that we were going to be getting new booths within two years,” he said. “Sure enough, about two years later, he asked me to start calling booth companies and talk to all of the manufacturers.
“We met with the reps and went to local shops to see each booth in action. USI North America has a great reputation for making the ultimate spray booth. We were immediately impressed by their durability and construction, not to mention all of their high-tech features.”
At a shop that fixes more than 150 vehicles every month, Lendino needed more than just one booth. He needed a system, and USI helped him fulfill all of his specific needs, Lendino said.
“USI allowed me to set up the booths the way I wanted them, including the lighting packages and several other features that are ideal for our production process,” he said. “One of our USI booths is a Chronotech (14’ x 30’), so I can fit dualies and larger trucks in there with an upgraded lighting package, including corner lights. My other booth is a double booth (26’ x 27’), where we can do even larger jobs. We have a curtain in the double booth, which means that we’re never limited by space, because we can paint three cars at the same time if we’re really busy.”
USI North America’s EPS System is saving Lendino a lot of time, which is quite important to any high-production shop, he said.
“Per vehicle, we’re saving roughly 25 minutes every cycle, which is definitely significant,” he said. “Essentially, you enter the job’s parameters in the system and it tells you the best way to paint the car.
In Florida, one of the most humid states in the country, a booth’s airflow is vital, especially for a shop that sprays a waterborne product.
“I hate those standup blowers and I’m so happy that we don’t ever need them with our USI booths,” Lendino said. “A lot of other booth manufacturers want all these fans and blowers all around, and all they do is really just spread dust throughout the booth. The great thing about these booths is that they accelerate the cure cycle and it cures the paint through proper airflow, which is all you need with water. It allows me to get the cars in and out of the booth faster and I never have to worry about whether they’re dry or not. It’s not even an issue.”
Backed by strong support and customer service from USI North America, Lendino knows that when he encounters any issues, he will get prompt and precise answers every time.
“Chris is our technical guy and he has the ability to diagnose any problem remotely, which is a big deal,” Lendino said. “He can get into our system and diagnose the situation without having to come here. He can guide me through things, educate us and get us back up and running right away. If there’s an issue that we can’t solve that way, they send me the parts the next day and we never miss a beat.”
Martin’s Collision Center
Location: Sanford, FL
(407) 323-7075
sanfordpaintandbody.com
Company At A Glance...
Type: Collision Repair
Facility Employees: 20
In Business Since: 2001
Number of Locations: Two
Combined Production Space: 20,000 square feet (combined)
USI of North America
Company Contact: Stefano Moretto
s.moretto@usius.com
(201) 405-7760
www.usius.com
To read more body shop profiles like this and stay current on collision repair industry news, visit autobodynews.com.
Sign up to receive Autobody e-News.
For more information, contact Bill Pierce, Digital Marketing Manager at Autobody News magazine.
Source: Autobody News
Share: